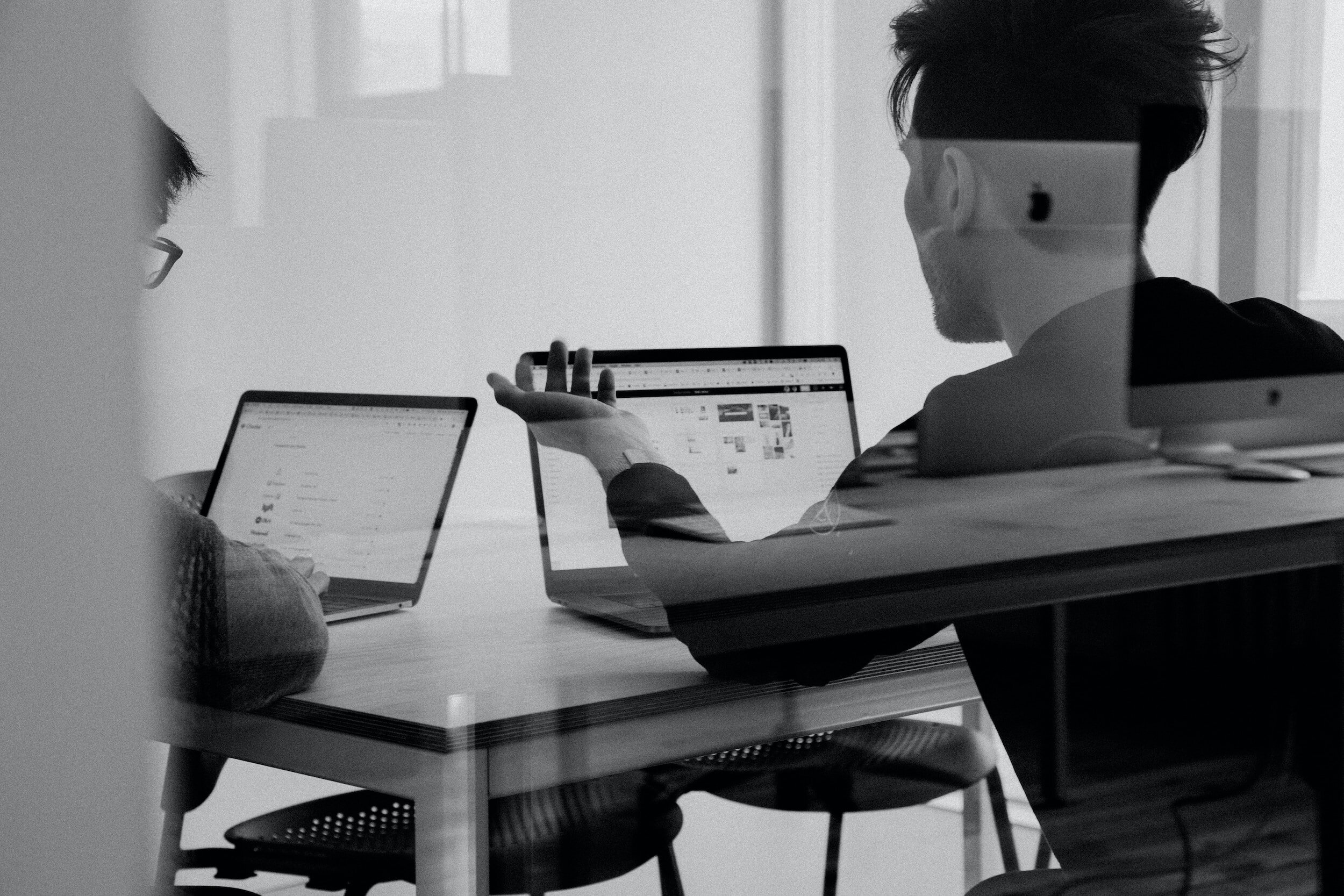
TRCG Success:
High Recall Volume
Challenge
A large medical device business was experiencing a high volume of software based product quality issues with a newly launched product, but their internal assessments concluded their quality system was performing adequately.
Solution
OUR ASSOCIATES PERFORMED AN ASSESSMENT TO ASSESS THE FOLLOWING:
Risk of reactive inspection from externally visible signals
Audit risk of product quality situation
The Quality System’s ability to manage product quality issues
Outcome
We were able to determine that externally visible signals could lead to a reactive inspection based on likely analysis methodologies.
Our teams determined that if a reactive inspection was initiated, the risk to the business was very high and could lead an inspector to believe the organization could not effectively correct or prevent issues, presenting a continued unacceptable safety risk to patients and users and the perception of repeat recalls for a single software defect.
We determined that while the organizations QMS was driving the generation of necessary objective evidence to support the resolution of issues; key personnel and processes were ineffectively performing corrective and prevention steps, resulting in multiple design changes to resolve a single software defect.
Subsequent to our engagement, an FDA reactive inspection was initiated and the business was able to successfully navigate the inspection thanks to the support and preparation enabled by our engagement.